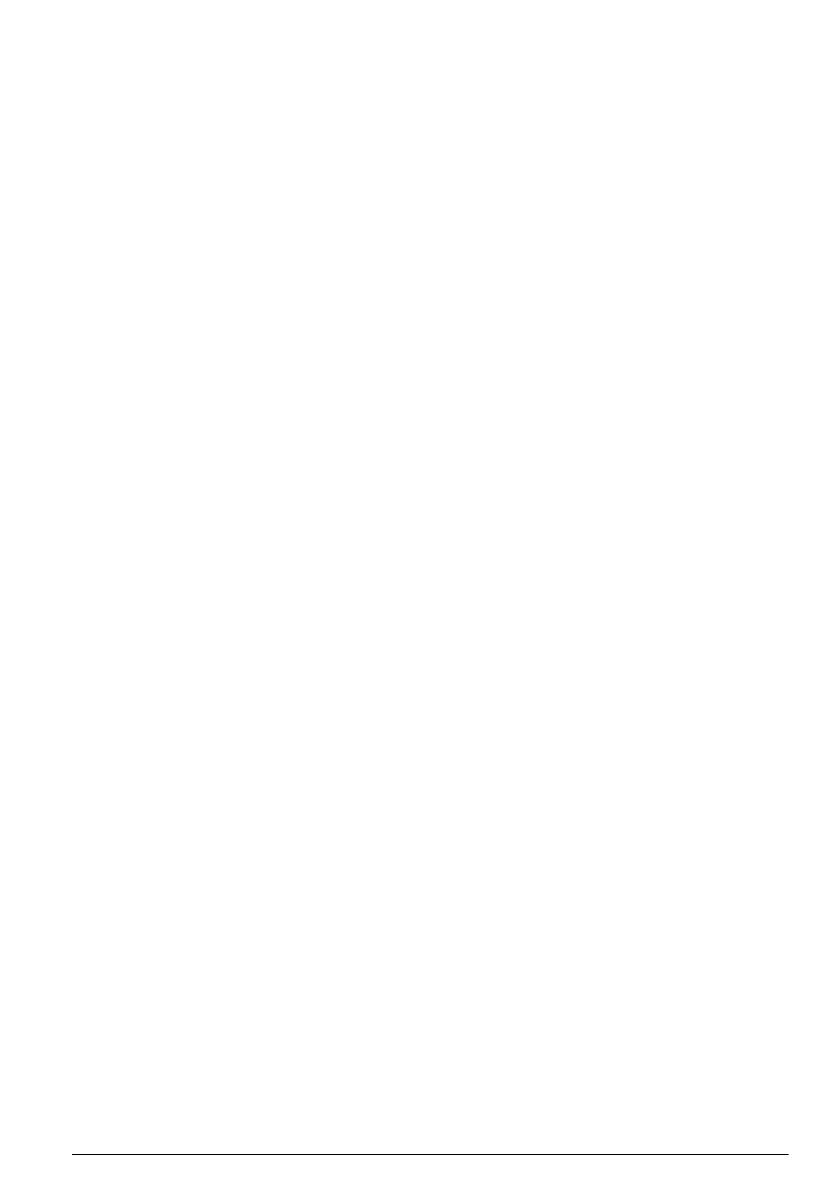
Model 29972
Model 29972 measures gas concentrations in beer or carbonated liquids. There are two models:
• Model 29972 is used with an electrochemical (EC) sensor.
• Model 29972.M is used with a luminescent dissolved oxygen (LDO) sensor.
The two models include the piercing head model 29974 pre-assembled. Refer to photo Q in Figure 2
on page 6.
The piercing needle assembly (Q3 in Figure 2 on page 6) pierces cans, metal or plastic caps or
crowns used in the beer industry. The piercing assembly has a piercer tube surrounded by a rubber
seal (Q4 in Figure 2 on page 6) for a perfect sealing between the bottle cap and the external
medium, within which the stainless steel cylindrical sampling tube can move. There are two types of
piercing knifes (Q35 in Figure 2 on page 6):
• Model 28072 for piercing metal caps
• Model 29979 for piercing PET bottles or plastic caps
Theory of operation
The beverage package sampler is used with an ORBISPHERE indicating instrument for analysis of
the oxygen, carbon dioxide and/or nitrogen gas content of a beverage. The ORBISPHERE indicating
instrument is supplied separately.
The indicating instrument reads and shows the measurement data from the package sampler sensor.
The indicating instrument is available in a portable, panel or wall mount version. Different indicating
instruments can be used. Refer to the indicating instrument documentation for additional information
(e.g., installation procedures, electrical connections).
The beverage package sampler holds the package sample being analyzed. A separate supply of
forcing gas moves the package liquid to the flow chamber, where the senor is installed. The sensor
and flow chamber are installed on the side of the sampler in a special sensor holder. The flow
chamber pulls liquid samples from the beverage sampler (e.g., bottle, can) to the sensor for analysis.
Different types of flow chambers are available for the different beverage package sampler
applications. The indicating instrument senses and shows on the display the package gas
concentration. The complete system supplies electrical and liquid connections to the instrument, to
the sensors and to the gas supplies.
Note: This manual is applicable to the ORBISPHERE Beverage Package Sampler models 29971 and 29972. Refer
to the user manual supplied with the gas analyzer indicating instrument that is used with the beverage package
sampler.
Product components
Make sure that all components have been received. If any items are missing or damaged, contact the
manufacturer or a sales representative immediately.
• Beverage package sampler
• Flow chamber
• Package sampler sensor: The sensor supplied is based on the instrument model and the beverage
sampler application. One of the package sampler sensors that follow:
• Electrochemical (EC) sensor for dissolved oxygen
• Luminescent Dissolved Oxygen (LDO) sensor
• Carbon dioxide (CO
2
) sensor
• Nitrogen (N
2
) sensor
• Plastic tubing for liquid connections, 5 m (16.40 ft)
English
7