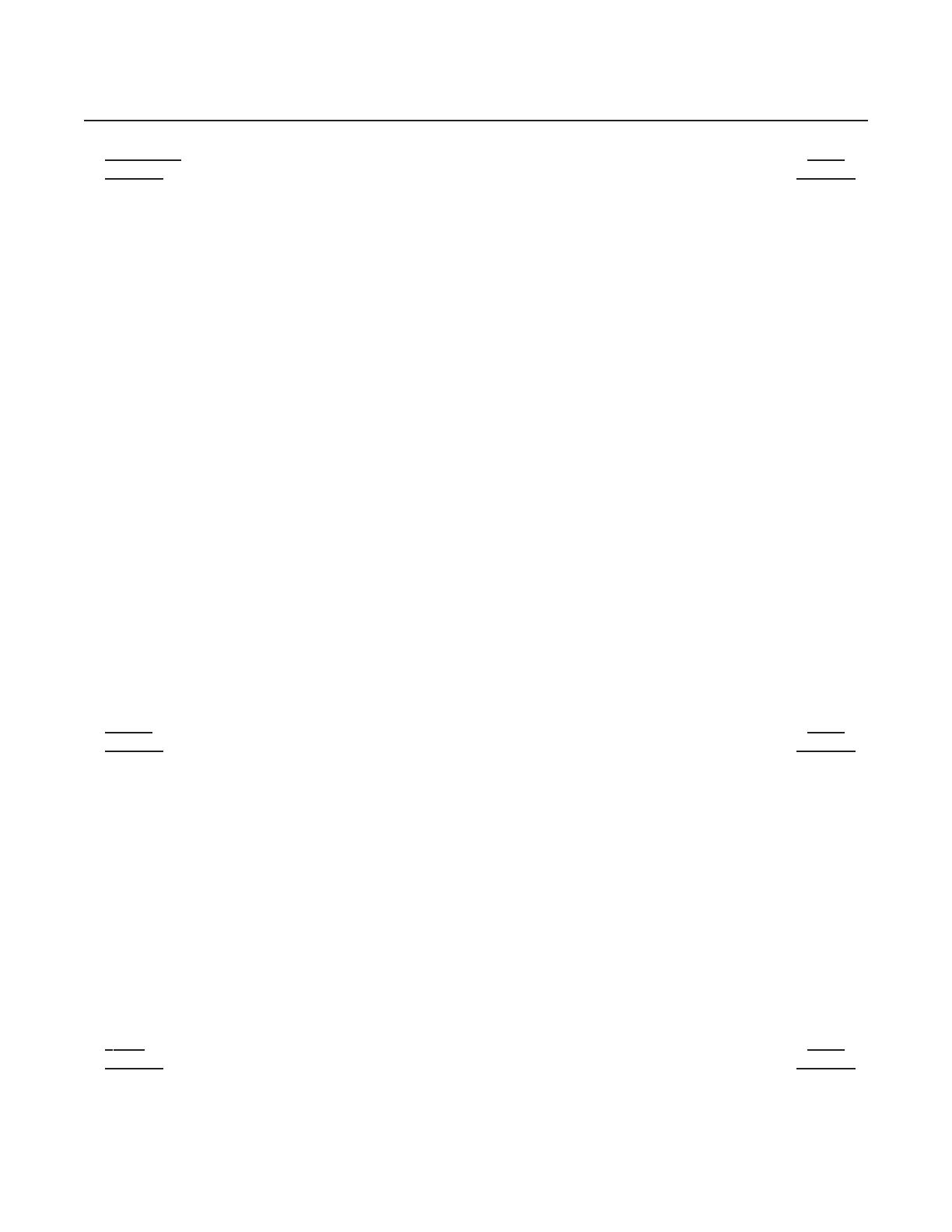
i
Contents
Installation and Operation Manual
X-VA-FC-eng
Part Number: 541B045AAG
December, 2015
Flow Controllers for Gas and Liquid Service
Paragraph Page
Number Number
Introduction Section 1
1-1 Description .....................................................................................................................................1-1
1-2 Design Features .............................................................................................................................1-1
1-3 Specifications .................................................................................................................................1-1
Installation Section 2
2-1 General ..........................................................................................................................................2-1
2-2 Receipt of Equipment .....................................................................................................................2-1
2-3 Recommended Storage Practice....................................................................................................2-1
2-4 Return Shipment ............................................................................................................................2-2
2-5 Transit Precautions.........................................................................................................................2-2
2-6 Removal from Storage....................................................................................................................2-2
2-7 Installation ......................................................................................................................................2-3
2-8 Panel Mounting...............................................................................................................................2-3
Operation Section 3
3-1 Operating Precaution......................................................................................................................3-1
3-2 General ..........................................................................................................................................3-1
Maintenance Section 4
4-1 General ..........................................................................................................................................4-1
Section A Essential Instructions
Essential Instructions......................................................................................................................A-1
Warranty, Local Sales/Service Contact Information ....................................................................... Back Cover
FIGURES
Figure Page
Number Number
1-1 Cutaway View, Principle of Operation .............................................................................................1-5
1-2 Cutaway View, NRS Valve ..............................................................................................................1-5
1-3 Cutaway View, cartridge Valve ........................................................................................................1-5
1-4 Dimensional Drawing Model FC 8744 ............................................................................................1-5
1-5 Dimensional Drawing Models FC 8802 and 8812 ...........................................................................1-6
1-6 Dimensional Drawing Models FC 8902 and 8912 ...........................................................................1-6
1-7 Dimensional Drawing Model FC 8842 ............................................................................................1-7
1-8 Dimensional Drawing Model FC 8942 ............................................................................................1-7
1-9 Dimensional Drawing Model FC 8845 ............................................................................................1-8
1-10 Dimensional Drawing Model FC 8945 ............................................................................................1-8
1-11 Dimensional Drawing Models FC 8805 and 8815 ...........................................................................1-9
1-12 Dimensional Drawing Models FC 8905 and 8915 ...........................................................................1-9
1-13 Dimensional Drawing Model FC 8830 ...........................................................................................1-10
TABLES
Table Page
Number Number
1-1 Flow Ranges ..................................................................................................................................1-3
1-2a Pressure/Temperature Ratings & Pressure Drop............................................................................1-3
1-2b Pressure/Temperature Ratings CRN ..............................................................................................1-3
1-3 Materials of Construction/ Connection/ Valve Option ......................................................................1-4
1-4 Model Code ...................................................................................................................................1-11
1-5 Sizing Chart ...................................................................................................................................1-13