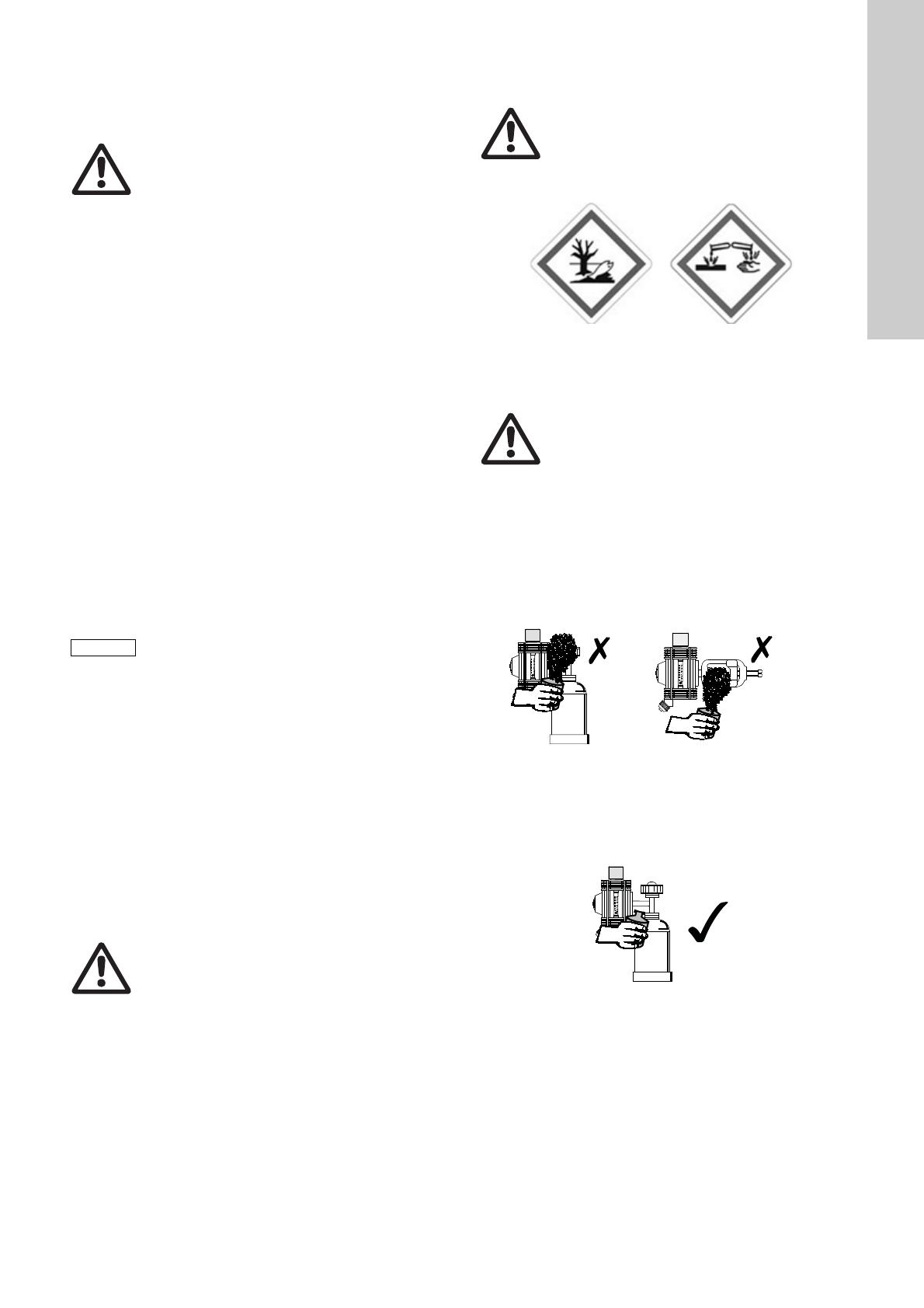
English (GB)
15
6.1 Checking the tightness
Due to the heavy corrosiveness of humid chlorine gas, all
leakages increase quickly. Therefore, even the smallest leakage
must be eliminated immediately.
6.1.1 Checking the chlorine solution lines and the injector
Observe the installation and operating instructions of the injector.
6.1.2 Checking the vacuum lines
Vacuum lines are all lines between vacuum regulator and injector.
1. Close all chlorine container valves.
2. Close the rate valve.
3. Open the shut-off valve at the injection unit.
4. Open the motive water valve.
5. Switch on the booster pump.
6. Open the rate valve.
– If the floater shows a gas flow, or the vacuummeter indicates
more than -9 m water column, the vacuum lines are leaky.
7. Close the rate valve.
8. Switch off the booster pump.
9. Close the motive water valve.
10. Close the shut-off valve at the injection unit.
11. Check the vacuum lines and connections. Re-tighten them
carefully, if necessary.
12. Repeat the tightness check.
– If the floater shows no gas flow, and the vacuummeter
indicates -9 m water column or less, the vacuum lines are
tight.
6.1.3 Checking the gas pressure lines
Gas pressure lines are all lines leading from the chlorine
containers to the vacuum regulator.
1. If the system is equipped with a nitrogen rinsing device, check
the tightness roughly with nitrogen.
2. Detailed checking is made with ammonia.
Checking the tightness with nitrogen
1. Close all chlorine container valves.
2. Open container connection valves and all shut-off valves up to
the chlorine gas dosing system.
3. Open the connection valve of the nitrogen cylinder.
4. Slowly open the valve of the nitrogen cylinder, until the lines
have a pressure of about 10 bar (read at the pressure gauge
of the vacuum regulator).
5. Apply soap water to all components under pressure.
– If bubbles form and/or pressure drops at the pressure
gauge, the pressure lines are leaky.
6. Depressurise the system.
7. Eliminate the leakage.
8. Repeat the tightness check.
9. If no bubbles form, and the pressure at the pressure gauge
does not drop significantly within one hour, the pressure lines
are tight.
Checking the tightness with ammonia
Fig. 13 Hazard notes for ammonia
Even very small leakages become evident with ammonia vapour,
which reacts with chlorine gas forming white mist.
Checking the pressure connections (after change of
container)
1. Open the container valve and immediately close it again.
2. Open the flexible plastic bottle filled with ammonia water.
3. Slightly press the bottle in a pumping manner, allowing the
ammonia mist to rise up. Slowly pass the open ammonia
bottle along gas-leading parts.
4. If white mist forms, the pressure connection is leaky.
Fig. 14 Ammonia and chlorine gas form white mist
5. Depressurise the system.
6. Eliminate the leakage.
7. Repeat the tightness check.
8. If no white mist forms, the pressure connection is tight.
Fig. 15 Pressure connection is tight
Warning
Check the tightness only if the entire system is ready
for start-up.
Danger of chlorine gas escape!
Reasons for insufficient operating vacuum:
Injector too small, defective, or blocked.
Booster pump too small, or defective.
Warning
Maximum nitrogen pressure 16 bar.
Danger of damages and leakages when exceeded.
Warning
Ammonia is irritating to eyes, respiratory system and
skin.
Ammonia is very toxic for water organisms.
When checking the tightness with ammonia, wear
tight protective goggles, gloves and clothes.
TM04 8410 2111
Warning
Liquid ammonia must not come in contact with lines
or parts of the system, because it is very corrosive.
Remove drops immediately with a dry cloth.
TM04 0710 0908TM04 0711 0908